The Challenge
TSC Subsea was contracted by a new client to carry out a multi-technology inspection campaign in the Southern North Sea to ascertain the integrity of subsea infrastructure. The inspection campaign covered multiple assets including gas lift risers, various nodal welds and a sponson.
The main challenge for this project was in the pre-engineering stages. It has always been difficult to provide constant scanning and data collection on small diameter pipe bends. The complex nature of the curvature requires careful mechanical manipulation to remain at a constant stand off and probe position as data is being collected. To address this and to acquire the nondestructive testing (NDT) data at the required level of accuracy, TSC Subsea developed a custom “extrados scanner” for the gas lift risers.
The Solutions
Due to the size and mix of inspections, multiple technologies were needed. As the risk-based inspection identified the potential of fatigue cracking and loss of wall thickness, TSC Subsea determined that a combined inspection strategy using Alternating Field Current Measurement (ACFM®) and Ultrasonic Phased Array (PAUT) would be the most appropriate technology.
Combining ACFM® and PAUT is a common approach to integrity assessment. Phased array is regarded as a volumetric method and is typically used to identify defects within the volume of the material and at the internal surface of the component. Defects such as corrosion, erosion and material inclusions are quickly identified and can be accurately reported for depth and position.
TSC’s proprietary ROV deployed ACFM® technology is a perfect complement to this as it is solely used to accurately detect linear type defects such as cracking that breaks the external surface of the component under test. Using the ACFM® and PAUT technologies together ensures total coverage and provides the extra confidence to perform fitness for service calculations.
ACFM® was used for the detection and sizing of any surface breaking fatigue cracks at nodal welds. Independent Probability of Detection (PoD) trials have proven ACFM’s advantages over competing technologies including Eddy Current (EC) and Magnetic Particle Inspection (MPI).
ACFM® was deployed using two field-proven ROV robotic scanning solutions – NodeScanner™ and MagCrawler™. Both systems are fitted with TSC Subsea’s latest array probes, offering high coverage which is essential for robotic scanning. The teach-and-learn 3 axis NodeScanner™ system offers diverless efficient scanning of complex geometries – capturing and streaming live, substantially more higher quality data per inspection point compared to alternative methods. The MagCrawler’s™ ability to drive to the inspection location after deployment enabled the ROV to deploy from a safe position. To add to the challenge, the MagCrawler™ was driven inverted, traversing the sponson to the inspection point.
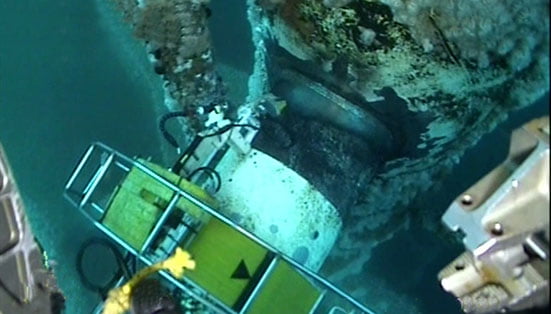
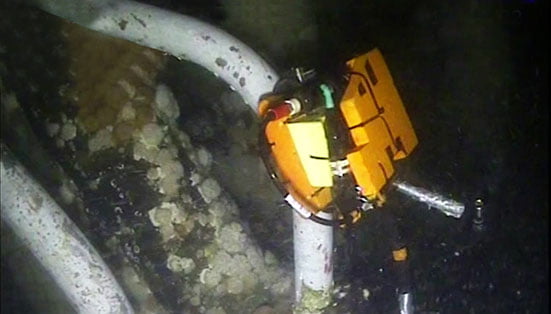
PAUT was deployed within the new extrados scanner by ROV for high resolution wall thickness measurements on the tight riser bends to provide high resolution thickness data and identify any potential areas of concern. This automated extrados scanner was developed specifically for this campaign, enabling remote deployment on the extrados of the 3” and 4” risers. It was capable of locating and tracking the extrados of the bend before scanning the high-risk inspection areas. The line scanner’s intuitive design included magnetic drive wheels, self-aligning to the bend radius which proved very successful.
The Result
Despite a small initial waiting-on-weather delay, the project mobilised from northern continental Europe and was successfully
completed in the allocated time and to the satisfaction of the end client.
Based on our world-leading position in diverless robotic inspection, combined with our broad services offering, TSC Subsea was able to support all aspects of the campaign. This gave the client a “one stop shop” solution and significant cost savings related to singlesource contracting were achieved. Contracting multiple inspection vendors would have substantially increased overall costs so this clearly demonstrates the cost saving benefits when planning multiple inspections across multiple assets via one key inspection vendor.
Further, as no divers were used during the campaign, the client was able to remove considerable potential risks by performing all inspection works by ROV combined with TSC Subsea’s remote robotic inspection methods. TSC Subsea’s comprehensive technology played a key part in the success of the campaign.
The challenge of scanning the extrados of piping is challenging, even in a topside environment. Because of our world-leading position in robotic inspections of subsea assets, as characterised by our ACFM® NodeScanner™ and MagCrawler™ systems, we had the necessary skills to develop the new LineScanner specifically to meet the needs of this campaign.
The new Phased Array LineScanner which is unique to, TSC Subsea is now included in TSC Subsea’s increasingly diverse portfolio of diverless non-destructive testing (NDT) solutions.